Infinity expands palletizer offerings with new Cobot palletizer
Infinity Machine and Engineering Corp. is proud to announce the newest addition to our line of palletizing solutions, the Infinity cobot.
Infinity’s cobot palletizer is engineered to increase productivity while seamlessly integrating with an existing workforce and facility.
Designed to stack finished product onto pallets for shipping or storage, the palletizer can complete its operations safely alongside a human workforce without the need for guarding or additional safety devices.
The advanced safety system of Infinity’s cobot can identify if someone or something is within the radius of its arm. If a person or object enters the cobot’s range of motion, the palletizer automatically reduces its speed to a crawl. If the arm of the cobot makes contact with the object, it immediately freezes in position.
Combine this sophisticated safety system with the cobot’s two standard build stations and operators are able to remove completed pallet stacks from the inactive build station while the machine is still in motion, allowing for optimal efficiency in the pallet building process.
Operator convenience is also prioritized in the palletizer’s design as key operating factors like recipe, product location, and product type can be modified directly from a touchscreen tablet.
The Infinity Cobot is set to redefine the efficiency of your operations with an advanced safety system allowing for uninterrupted production runs and improved operator convenience.
Since debuting our line of palletizing solutions in 2023, we have continuously looked for
ways to cater to the needs of our customers.
Infinity’s C15 casepacker provides functionality and sustainability with display ready trays
As ecological consciousness has continued to become more prevalent on a global scale, consumer data has clearly indicated individuals take their own environmental impact into account when making purchasing decisions.
In a 2020 consumer study conducted by McKinsey & Company, 78% of consumers indicated sustainability as an important factor of their lifestyle and more than 60% of consumers stated they would be willing to pay more for a product if it was packaged sustainably.
In consumer product industries like tissue, sustainable packaging creates an opportunity for product differentiation. If brands utilize sustainable packaging effectively, there is increased potential to establish and develop customer loyalty.
Infinity Machine & Engineering Corp. produces both multi-pack and single roll wrappers with a proven history of providing sturdy, sustainable, primary packaging for tissue rolls across a multitude of formats. Due to Infinity’s innovative packaging machinery, smaller packs of bathroom tissue and kitchen towel wrapped in paper overwrap are becoming increasingly more common in storefronts.
Despite the advantages of sustainable packaging, next time you go to your local supermarket, you may be surprised to see how little it is being utilized in large bundles of tissue products.
The immediate solution would seem to be replacing polyethene packaging with more sustainable paper overwrap, as it is done in smaller packs. However, large bundles of multiple tissue packs present additional challenges. The increased mass of bundles makes paper wrapped solutions much harder to implement effectively, especially when you consider the durability polyethylene provides.
Furthermore, the difference in material properties between paper wrap and polyethene would require new means of forming, sealing, and cutting bundles, which would require additional engineering and development.
Confronted by this dilemma, Infinity engineers further developed some of our existing capabilities to provide a more ecological alternative to polyethylene bundlers.
Since its debut in 2010, Infinity’s C15 casepacker has become a fixture of tissue packaging, with over 250 machines installed across six countries. Designed to provide secondary packaging for tissue, diapers and hygiene products, the C15 can pack product into corrugated cases or trays.
While cases are much more common, corrugated trays are becoming more frequently utilized due to the ecological benefits they offer. Corrugate trays can often be made using less than half the material of cases, with the C15 capable of loading trays with bottom gap flaps and a wall height as small as 100mm.
These trays can suitably support poly wrapped or paper wrapped packages and can be designed with easy open perforations for display. Some supermarket chains in North America have already begun to adopt these display ready trays.
The utility of these trays doesn’t end with display functionality. Utilizing trays instead of bundles for bulk tissue packaging creates a unique way to differentiate products, while also improving the sustainability of product packaging.
Innovative packaging solutions that prioritize the environment, like replacing plastic bundles with corrugate trays, ensure that sustainable packaging is not a trend, but rather an evolution of the industry. Infinity Machine and Engineering Corp. is committed to being at the forefront of this evolution, ensuring that our customers can prioritize sustainability and functionality.
Infinity expands product line to offer warehouse automation solutions
Throughout its 20-year history, Infinity Machine & Engineering Corp. has been a company committed to innovation, fine-tuning the design of automated tissue packaging machinery to best suit the needs of their customers. In its 20th year of operation, Infinity is embarking on another bold path, this time into warehouse automation.
Infinity’s line of warehouse automation solutions features a palletizer, a pallet conveyor, and seven different models of Automated Guided Vehicles (AGVs). Combined with Infinity’s comprehensive line of tissue packaging solutions, Infinity customers can have every process after the log saw completed by integrated machinery from a single supplier.
The AGVs offered by Infinity can perform a range of warehouse operations, across a variety of industries. Infinity’s fleet includes a small, AMR-style AGV, four fork truck models, including an outrigger model with a small turning radius, a narrow-bodied model that can easily maneuver throughout a warehouse, a single double vehicle that can transport two pallet stacks at once, and a forklift designed specifically for Over the Road (OTR) trailer loading and unloading. Infinity also offers two AGVs designed for raw material transport, a cradle-style vehicle, capable of omnidirectional travel, and also a counterbalanced clamp vehicle.
Infinity pallet conveyor systems boast a wide range of conveyor sections that ensure that the pallet sorting process is streamlined. Each line of conveyor can be customized to the unique requirements of the customer’s operations. These conveyor sections include pallet squaring units, pallet destacking/restacking units, pop-up transfers, and pallet rotating conveyor.
Similar to the Infinity pallet conveyor, Infinity palletizers are made up of modular sections that can be arranged into countless layouts. The flexibility created by Infinity palletizers makes them perfect for a multitude of product lines, from single products to large-scale, multi-line operations. Infinity palletizers offer fully servo, fully automatic stretch wrapping, slip sheet placement, and an integrated labeler.
Infinity Releases Wrapper for Wide Diameter Rolls
International leader in automated tissue packaging machinery, Infinity Machine & Engineering Corp. has released the new VGXL multipack wrapper, a machine capable of producing multi-roll packs as wide as 720mm.
Based on the robust design of Infinity’s VISION G3 multipack wrapper, the VGXL shares attributes that have made the VISION G3 famous, like top and bottom infeed belts, and an accessible design that allows for simplified maintenance.
The VGXL is the result of Infinity recognizing consumer preferences shifting towards purchasing larger, wide-format rolls. As consumer trends continue to evolve, tissue packaging machinery must adapt to enable consistent, high-quality packaging of these wider rolls. The VGXL is the perfect machine to serve this growing sector of the market.
Infinity releases R10SW Palletizer
It is no secret that in recent decades manufacturers have pivoted toward automating the production process at a rapid pace. And as the cost of labor has steadily increased, there is no indication this shift toward automation will slow down anytime soon.
Tissue converters have been especially proactive in implementing automation into their production process as nearly every step of the converting process can and has been automated.
In 2004, Infinity Machine & Engineering Corp. was founded in response to the surge in automated tissue converting lines and has led the charge in automating the tissue packaging process ever since.
Already boasting the most comprehensive roster of automated packaging machinery in the industry, Infinity is further expanding their roster of automated machinery to cover the end of the production line with the R10SW palletizer.
Responding to consumer demand, the R10SW palletizer can be integrated with Infinity packaging lines, enabling Infinity machinery to automate every step of the tissue production process after the log saw.
A key aspect of the R10SW palletizer is its modularity. The R10SW is made up of modular palletizer sections that can be arranged into countless different layouts to accommodate production requirements, as well as facility limitations. The flexibility created by these palletizer sections makes it perfect for a multitude of product lines, from single products to large-scale, multi-line operations.
The palletizer segments offered by Infinity include automatic slip sheet placement, integrated labeling, and fully automatic, fully servo stretch wrapping. All are designed to provide extreme efficiency and versatility in a minimal amount of space.
The R10SW palletizer comes equipped with an articulated robot arm from FANUC, one of the world’s largest industrial robot manufacturers. The R10SW’s FANUC articulated robot arm is capable of quick cycle times and robust performance. The development of the R10SW palletizer has led to Infinity being an official “FANUC Authorized System Integrator”.
Extreme versatility is built into the design of the R10SW, either vacuum or servo gripper end effectors can be equipped on the palletizer, allowing for high-speed stacking capabilities on a wide range of products, including cases, bundles, and DRP.
The versatility of the R10SW is complemented by robust performance as the palletizer has a full unit load total height of 110 inches.
Infinity engineers prioritized operator convenience and safety in the design of the R10SW, resulting in a machine that is as safe as it is accessible. The palletizer features multiple safety zones, separated by access gates, allowing for safe up-close monitoring of production. Access to hard-to-reach areas of the machine has also been improved.
As tissue converters throughout the world continue to embrace automation, flexibility is as essential in the production’s end-of-line as it is in the converting and packaging process. The R10SW brings Infinity’s signature innovative engineering and robust build quality to the world of palletizing solutions, making the production end-of-line safer, smarter, and as flexible as the rest of your line.
Infinity Debuts New Pivoting Servo Merge Diverter
Infinity Machine & Engineering Corp. is proud to release the newest addition to its line of servo diverters, the Pivoting Servo Merge.
Specifically designed for facial tissue converting lines, the PSM diverter merges two layers of product into one layer, or one layer of product into two, ensuring a balanced, precise output for production.
The PSM features fully automatic guardrails, ensuring changeovers between flat tissue packs and cube tissue packs are simple and quick.
Another aspect of the PSM that puts customer convenience at the forefront is the machine’s ability to operate with its own individual PLC, or to be integrated with an existing PLC. Whatever a converting line requires, the PSM can be incorporated with ease.
Infinity’s newest diverter also features electronic gearing, allowing the operator to have complete control over the gap size between packs, and in turn, control over product orientation. With the PSM, product is merged, distributed, and controlled all in one compact space.
The PSM diverter from Infinity is the perfect distributor to make facial tissue lines faster, smarter, and more versatile.
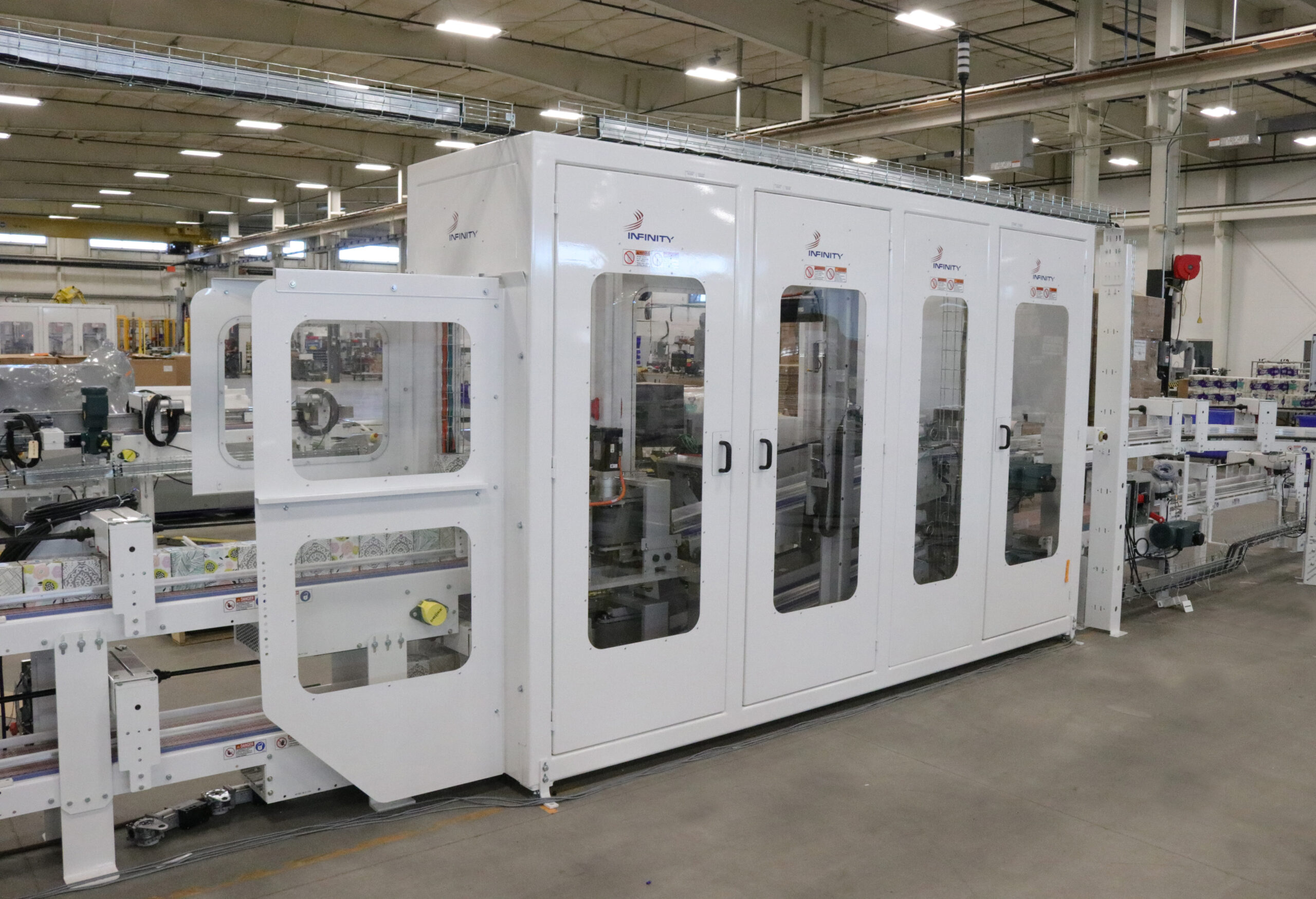
Infinity’s Optic M1 poly bundler offers unmatched versatility and unmatched performance.
Since our inception in 2003, Infinity Machine and Engineering Corp. has been committed to reshaping the Tissue packaging industry. With a focus on superior build quality, and devoted customer service, Infinity has become a trusted name in packaging machinery throughout the world. We have been privileged to install our machinery in over 20 countries across every continent except Antarctica. With our eye on the global community we serve, Infinity is proud to announce the release of our Optic M1 Bundler, designed from the ground up with the needs of the international market in mind.
The Optic M1 Bundler can produce a wide range of bundle configurations and reach speeds of over 20 bundles per minute, giving it the versatility and speed to disrupt the tissue bundler market. Other key advantages of the Optic M1 are its small footprint, robust steel frame, auto splice poly unwind, active vacuum lance, quick change knife and modular capability.
At the Infeed of the machine, the Optic M1 features an integrated two-stage choke belt diverter, with hand wheel adjustment for pack width. The Optic also features the same Infeed as our Infinity casepackers, creating the added benefit of common parts and common machine knowledge for maintenance technicians. Also, the only wear part on the infeed of the machine are the infeed belts, further reducing machine maintenance.
The Optic M1 features Flight Bars that are synchronized with the indexer, enabling maximum take over speed. The additional flight bar on the Optic M1 is the perfect tool for stacked, “core up” roll configurations. However, to allow for maximum versatility, the second flight bar can be removed and an upender can be swapped in. The upender enables the machine to bundle rolls stacked on ends, so that the Optic M1 can bundle a vast array of configurations between the two roll stack orientations. Furthermore, both the second flight bar and the upender units are on casters allowing for quick and easy swaps between the two.
The Unwind of the Optic M1 is servo driven to ensure easy poly position adjustment. Poly can also be wound from the front or back of the reel, simplifying the loading process. A Poly pullout cart is also featured on the Optic M1, simplifying the process of poly loading and unloading.
A ubiquitous feature on Infinity bundlers is our standard vacuum lance. On the seal jaw of the bundler, the vacuum lance sucks out excess air from the bundle, creating crisp, tight bundles every time. The Seal Jaw also offers a quick-change knife and seal jaw replacement, reducing machine down time.
Infinity engineers have prioritized reducing the time and cost of machine maintenance in the design of the Optic M1, resulting in a machine with very few wear parts and many automatic adjustment features. The only manual lubrication axes are the top/bottom seal jaw, cassette width adjustment and the cassette raise/lower, all bearing are lubed for life. The only wear parts of the machine are the indexer belts, Cassette/Flight bar timing belts and seal wire. The Optic M1 also features only one valve bank with ethernet feedback, and only three manual adjustments. Most adjustments on the Optic are done automatically by utilizing adjustment motors. Celling height, exit guides and cassette backstop are all adjusted automatically.
A defining feature of the Optic M1, that truly sets it apart from other bundlers on the market is its modular capability. Since 2005, Infinity has manufactured bundlers with its industry original Infusion modular system. Designed to overcome the limitations of fixed linear machines, the Infusion modular system allows for different machine units, such as a bundler, bagger or casepacker to be attached to a common infeed module via fixed docking stations. This process can be completed in a half hour and gives our customers the ability to reduce their capital investment and more efficiently utilize floor space.
Accessibility was at the forefront of our engineer’s minds while designing the Optic M1. The pusher on the machine is on a vertical adjustment, which keeps the working height of the machine low, while also increasing the number of pack configurations the machine is capable of. The vertical adjustment also allows for a simplified change to a casepacker module if desired. The modules on the machine feature a French door design, which increases ease of access to machine components. And the discharge of the Optic M1 features a tip down exit gate, improving worker mobility around the machine.
Featuring a more accessible design, versatile performance, and Infinity’s signature robust steel framing, the optic M1 poly bundler is our most advanced poly bundler yet. Look no further because the future of packaging is staring you in the face.
Infinity Servo Diverters Enable Ultimate Line Optimization
As the tissue-converting industry continues to experience increased growth, flexibility is no longer a goal of converting lines, it is a necessity.
Converters need to offer lines with optimized speed and diverse products to keep up with consumer preferences and demand. Infinity’s line of servo diverters meets and surpasses this need for flexibility.
All four models of Infinity servo diverter can act as the central brain of a converting line, efficiently balancing incoming product to the required downstream machinery while ensuring a steady, even flow of product.
Infinity diverters also help reduce the need for excess conveyors and additional floor space by utilizing precise, variable control. The diverter’s ability to merge, distribute and control makes them the smartest, most flexible diverters on the market.
Each of Infinity’s diverters can accommodate unique needs for different converting lines. The Telescopic Servo Merge diverter, or TSM, is specifically designed to balance converting lines from four lanes to three or two lanes.
The Quick Switch diverter is similar to the infeed indexers that appear on most of Infinity’s casepackers and bundlers. It is offered as a one, two, or three-arm diverter that usually takes packs or roll products and distributes them to the necessary lanes.
Infinity designed its Single Roll Laner diverter to be the perfect fit for lines with a multipack wrapper and single roll wrappers. The SRL diverter sets the industry standard for diverters that distribute four lanes to five, six, or even seven lanes.
Featuring a unique servo-controlled pivoting system, Infinity’s C2L diverter is a great fit for lines with dual packaging legs and one log saw. The C2L diverter can take four lanes and distribute to two layers of four-lane conveyor.
Some additional key features that make Infinity diverters the best on the market are a discharge lane selection on the HMI as well as a toolless changeover.
With four unique models of diverter, Infinity Machine & Engineering can provide the perfect solution to make your line faster, smarter, and more flexible.
Eliminating Machine Maintenance Downtime
With around-the-clock automated operation quickly becoming the global norm in production lines, the negative effects of unscheduled machine downtime become increasingly more pronounced.
High-quality machinery is no longer enough, production lines need reliable customer service and quick turnarounds. This is why Infinity Machine & Engineering’s technical services are designed not just to resolve unplanned maintenance issues but eliminate them entirely.
Infinity prides itself on offering a range of preventative maintenance plans to keep machines and the companies that own them at optimal performance. A fixture of these plans is onsite machine audits performed quarterly, semiannually, or annually. These audits include a thorough inspection of all machines, documented service reports with recommendations after each visit, and additional machine training after the audit’s completion.
However, Infinity’s preventative maintenance begins before the machine leaves the facility. Every machine built by Infinity is put through a rigorous factory acceptance test, testing the customer’s exact specifications, and often running the customer’s actual product. This process ensures the machine is ready for installation and operation as soon as it is delivered. Furthermore, Infinity’s staff boasts a combined 65 years of packaging machinery installation experience, ensuring machine installation time is reduced to a minimum.
Another customer-focused technical service Infinity offers is operator and maintenance technician training. Technician training can be customized based on customer needs, including mechanical training on the customer’s existing Infinity
equipment, and electrical and E&I training. Offerings for Mechanical training include mechanical prints, parts search, rebuilding of assemblies, maintenance inspections, and lubrication routes. Electrical training covers electrical prints, parts search, PLC troubleshooting, replacement parts, and inspections.
To accommodate the round-the-clock production schedule of our customers, Infinity provides 24/7 on-call customer service. Field services techs can be at a customer’s mill within 24-36 hours after a call. Furthermore, Infinity does not charge extra for weekend work from their field service techs, whereas other
companies often charge double time on Sundays.
Another facet of Infinity’s technical services is an extensive spare part inventory. Between their Bologna and Green Bay facilities, Infinity has 20,000 spare parts on hand. There is also a dedicated expedited shipper for emergency situations so
crucial parts can be ordered at a moment’s notice.
Infinity takes consumer convenience in spare part offerings to the next level with predictive maintenance part kits. Through engineering, parts research, and mechanical knowledge of equipment, these kits are designed to maintain full runnability without unplanned downtime. Infinity’s predictive maintenance part kits are customized with common wear parts for all Infinity machine models. These kits also include a parts breakdown list, mechanical prints, and a standard procedure manual to assure the work is done to OEM spec. These give technicians the proper paperwork and parts to ensure the job will be completed properly and in a timely manner.
Infinity was created with a simple vision, to serve the customer, and the technical services offered by Infinity embody that vision. Machine audits that identify issues before they happen, a dedicated 24/7 customer support team, and an extensive spare part inventory all contribute to making this vision reality. When you buy Infinity, you buy peace of mind.
Infinity Poly Bagger redesign decreases machine footprint, increases machine production.
While not as conventional as poly bundles, poly bags have unique benefits and applications for tissue product packaging. While bundles are suitable for rolled product, folded product like napkins are too unstable and need to be packaged in poly bags. However, Poly bags are not only for folded products, they are also often used on industrial rolls as the bag end seals are easy to open and are better looking than bundle seals. While poly bags are versatile, the packaging machines that utilize them are not. Most poly baggers on the market today have a long, belted wicket in order to move poly bags to the machine loader. These wickets jut out from the side of the machine and are often 10 feet (3 meters) long. Because of the wicket’s large size and awkward placement, these machines take up a large amount of floor space and can greatly reduce the accessibility of a facility. In addition to this, the traditional belted wicket system has a limited capacity of bags that can be loaded at a time, reducing bagging efficiency.
However, Infinity Machine & Engineering Corp. has retooled their poly bagger to eliminate these major drawbacks. Infinity has developed a multi-shelf wicket system for their G10 and G20 poly baggers that eliminates nine feet of wicket length and simultaneously increases poly bag capacity. The new multi-shelf wicket system features seven shelves that can each be filled up to two inches high with poly bags. When one shelf is empty, the machine automatically retracts the shelf and replaces it with a full one. The switch cycle for the Infinity multi-shelf wicket system is also comparable to that of traditional belted wickets, as shelves are swapped and back in production in 15 seconds. Empty retracted shelfs are annunciated by an illuminated signal and can be restocked with bags safely and efficiently while the machine is in operation.
The compact design of the multi-shelf system eliminates a roughly three feet by nine feet section of machine, dramatically decreasing the amount of space needed to accommodate a poly bagger. The trays on Infinity’s new wicket system are also length adjustable, allowing the machine to run shorter poly bags at higher speeds. While Infinity has radically improved the design of their poly bagger, the new multi-shelf wicket system is still compatible with Infinity’s signature Infusion 3 in 1 modular system. The new more efficient poly bagging module can be seamlessly swapped in and out of a common infeed with casepacking and bundling modules, creating the pinnacle of packaging diversity. Infinity’s latest innovation in tissue packaging machinery has finally enabled poly baggers to be as versatile as the packing they support. To learn more about Infinity’s new multi-shelf wicket system, schedule a meeting with the Infinity sales team today!