Infinity Machine & Engineering Corp. to exhibit at Tissue World 2025
From April 8 th to April 10 th , Infinity Machine & Engineering Corp. will return to the Messe Dusseldorf to exhibit at Tissue World 2025.
The previous edition of Tissue World took place last January in Miami and brought together professionals from across the American tissue industry. This year’s exhibition is expected to draw visitors from across Europe and will focus on future proofing the tissue industry for sustainable growth.
Since establishing a base for its European operations in Bologna, Infinity has developed a significant presence in Europe. In the last ten years, Infinity has sold over 120 units of machinery to customers across 15 European countries.
A key piece of Infinity’s machine catalog that has greatly contributed to its growth in Europe is the Optic M1 poly bundler. Designed with the unique needs of the European tissue market in mind, the Optic M1 boasts swappable flight bar and upender units. The interchangeable upender/flight bar units give the machine increased flexibility on the product infeed, allowing for the production of bundles with vertical and horizontal roll formats.
To learn more about the Optic M1, as well as Infinity’s entire roster of innovative tissue packaging machinery, be sure to visit Infinity’s booth at space F40.
Infinity’s C15 casepacker provides functionality and sustainability with display ready trays
As ecological consciousness has continued to become more prevalent on a global scale, consumer data has clearly indicated individuals take their own environmental impact into account when making purchasing decisions.
In a 2020 consumer study conducted by McKinsey & Company, 78% of consumers indicated sustainability as an important factor of their lifestyle and more than 60% of consumers stated they would be willing to pay more for a product if it was packaged sustainably.
In consumer product industries like tissue, sustainable packaging creates an opportunity for product differentiation. If brands utilize sustainable packaging effectively, there is increased potential to establish and develop customer loyalty.
Infinity Machine & Engineering Corp. produces both multi-pack and single roll wrappers with a proven history of providing sturdy, sustainable, primary packaging for tissue rolls across a multitude of formats. Due to Infinity’s innovative packaging machinery, smaller packs of bathroom tissue and kitchen towel wrapped in paper overwrap are becoming increasingly more common in storefronts.
Despite the advantages of sustainable packaging, next time you go to your local supermarket, you may be surprised to see how little it is being utilized in large bundles of tissue products.
The immediate solution would seem to be replacing polyethene packaging with more sustainable paper overwrap, as it is done in smaller packs. However, large bundles of multiple tissue packs present additional challenges. The increased mass of bundles makes paper wrapped solutions much harder to implement effectively, especially when you consider the durability polyethylene provides.
Furthermore, the difference in material properties between paper wrap and polyethene would require new means of forming, sealing, and cutting bundles, which would require additional engineering and development.
Confronted by this dilemma, Infinity engineers further developed some of our existing capabilities to provide a more ecological alternative to polyethylene bundlers.
Since its debut in 2010, Infinity’s C15 casepacker has become a fixture of tissue packaging, with over 250 machines installed across six countries. Designed to provide secondary packaging for tissue, diapers and hygiene products, the C15 can pack product into corrugated cases or trays.
While cases are much more common, corrugated trays are becoming more frequently utilized due to the ecological benefits they offer. Corrugate trays can often be made using less than half the material of cases, with the C15 capable of loading trays with bottom gap flaps and a wall height as small as 100mm.
These trays can suitably support poly wrapped or paper wrapped packages and can be designed with easy open perforations for display. Some supermarket chains in North America have already begun to adopt these display ready trays.
The utility of these trays doesn’t end with display functionality. Utilizing trays instead of bundles for bulk tissue packaging creates a unique way to differentiate products, while also improving the sustainability of product packaging.
Innovative packaging solutions that prioritize the environment, like replacing plastic bundles with corrugate trays, ensure that sustainable packaging is not a trend, but rather an evolution of the industry. Infinity Machine and Engineering Corp. is committed to being at the forefront of this evolution, ensuring that our customers can prioritize sustainability and functionality.
Infinity expands product line to offer warehouse automation solutions
Throughout its 20-year history, Infinity Machine & Engineering Corp. has been a company committed to innovation, fine-tuning the design of automated tissue packaging machinery to best suit the needs of their customers. In its 20th year of operation, Infinity is embarking on another bold path, this time into warehouse automation.
Infinity’s line of warehouse automation solutions features a palletizer, a pallet conveyor, and seven different models of Automated Guided Vehicles (AGVs). Combined with Infinity’s comprehensive line of tissue packaging solutions, Infinity customers can have every process after the log saw completed by integrated machinery from a single supplier.
The AGVs offered by Infinity can perform a range of warehouse operations, across a variety of industries. Infinity’s fleet includes a small, AMR-style AGV, four fork truck models, including an outrigger model with a small turning radius, a narrow-bodied model that can easily maneuver throughout a warehouse, a single double vehicle that can transport two pallet stacks at once, and a forklift designed specifically for Over the Road (OTR) trailer loading and unloading. Infinity also offers two AGVs designed for raw material transport, a cradle-style vehicle, capable of omnidirectional travel, and also a counterbalanced clamp vehicle.
Infinity pallet conveyor systems boast a wide range of conveyor sections that ensure that the pallet sorting process is streamlined. Each line of conveyor can be customized to the unique requirements of the customer’s operations. These conveyor sections include pallet squaring units, pallet destacking/restacking units, pop-up transfers, and pallet rotating conveyor.
Similar to the Infinity pallet conveyor, Infinity palletizers are made up of modular sections that can be arranged into countless layouts. The flexibility created by Infinity palletizers makes them perfect for a multitude of product lines, from single products to large-scale, multi-line operations. Infinity palletizers offer fully servo, fully automatic stretch wrapping, slip sheet placement, and an integrated labeler.
Infinity Releases Wrapper for Wide Diameter Rolls
International leader in automated tissue packaging machinery, Infinity Machine & Engineering Corp. has released the new VGXL multipack wrapper, a machine capable of producing multi-roll packs as wide as 720mm.
Based on the robust design of Infinity’s VISION G3 multipack wrapper, the VGXL shares attributes that have made the VISION G3 famous, like top and bottom infeed belts, and an accessible design that allows for simplified maintenance.
The VGXL is the result of Infinity recognizing consumer preferences shifting towards purchasing larger, wide-format rolls. As consumer trends continue to evolve, tissue packaging machinery must adapt to enable consistent, high-quality packaging of these wider rolls. The VGXL is the perfect machine to serve this growing sector of the market.
South Korean Tissue Manufacturer Increases Investment in Infinity Machinery
MSS Holdings of South Korea has purchased its third packaging line from international leader in automated tissue packaging machinery, Infinity Machine and Engineering Corp.
This most recent investment in Infinity equipment by MSS Holdings is the company’s second Infinity packaging line purchased for their brand Monalisa.
Infinity will be providing an EPXL poly bundler, VISION G3 multipack wrapper, and conveyor system for the project.
The EPXL poly bundler features a wide frame that allows the machine to create wide format packs, which are common in the South Korean market. Additionally, the EPXL also boasts an integrated diverter and flight bar for simplified product collation, and an automatic poly pull out cart for safe and convenient poly loading.
MSS Holdings selected the VISION G3 multipack wrapper for their new packaging line as Infinity’s most advanced wrapper. The VISION G3 Infinity will be supplying to MSS Holdings will feature an external handle applicator, giving MSS holdings the ability to differentiate their product with increased consumer convenience.
Infinity has steadily increased its influence in the Asian tissue market as Infinity packaging machinery is operated across South Korea, Thailand, Indonesia, and the Philippines.
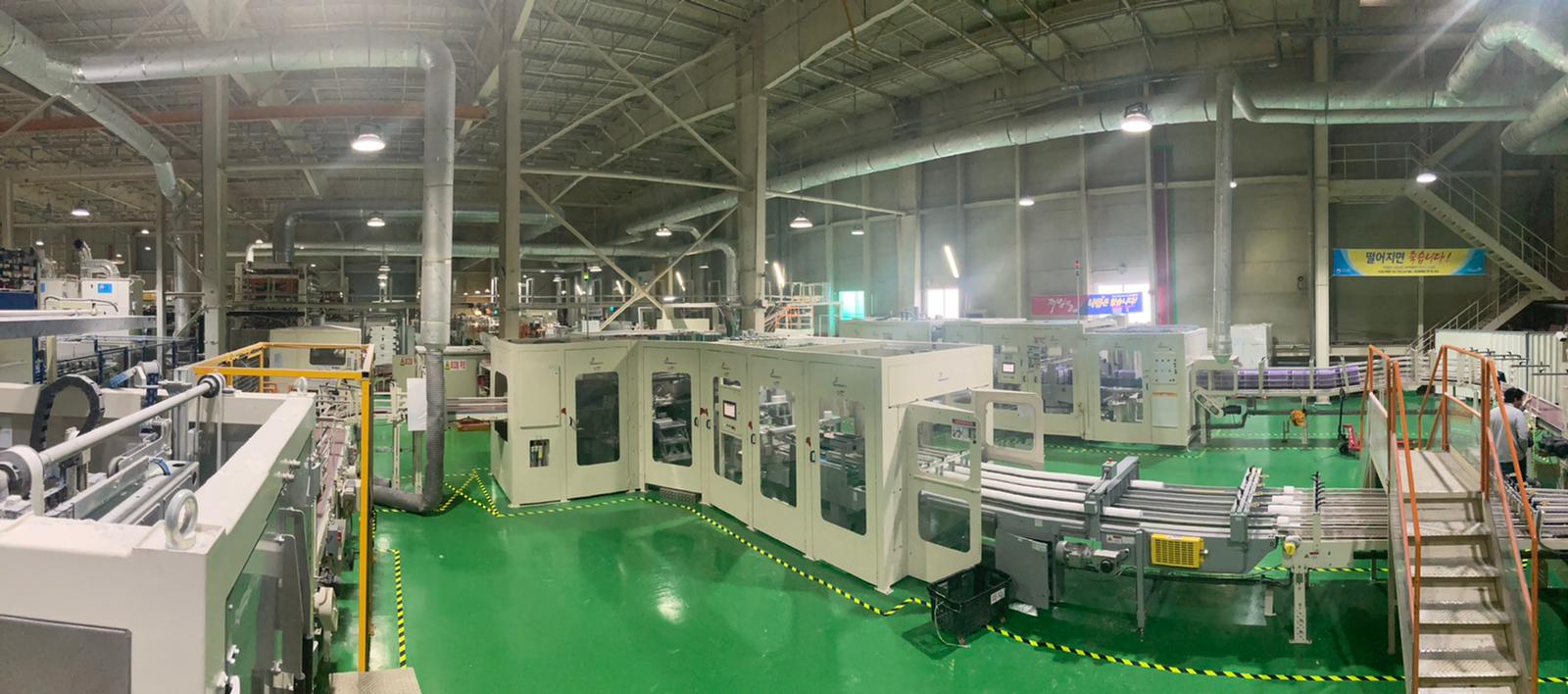
Infinity releases R10SW Palletizer
It is no secret that in recent decades manufacturers have pivoted toward automating the production process at a rapid pace. And as the cost of labor has steadily increased, there is no indication this shift toward automation will slow down anytime soon.
Tissue converters have been especially proactive in implementing automation into their production process as nearly every step of the converting process can and has been automated.
In 2004, Infinity Machine & Engineering Corp. was founded in response to the surge in automated tissue converting lines and has led the charge in automating the tissue packaging process ever since.
Already boasting the most comprehensive roster of automated packaging machinery in the industry, Infinity is further expanding their roster of automated machinery to cover the end of the production line with the R10SW palletizer.
Responding to consumer demand, the R10SW palletizer can be integrated with Infinity packaging lines, enabling Infinity machinery to automate every step of the tissue production process after the log saw.
A key aspect of the R10SW palletizer is its modularity. The R10SW is made up of modular palletizer sections that can be arranged into countless different layouts to accommodate production requirements, as well as facility limitations. The flexibility created by these palletizer sections makes it perfect for a multitude of product lines, from single products to large-scale, multi-line operations.
The palletizer segments offered by Infinity include automatic slip sheet placement, integrated labeling, and fully automatic, fully servo stretch wrapping. All are designed to provide extreme efficiency and versatility in a minimal amount of space.
The R10SW palletizer comes equipped with an articulated robot arm from FANUC, one of the world’s largest industrial robot manufacturers. The R10SW’s FANUC articulated robot arm is capable of quick cycle times and robust performance. The development of the R10SW palletizer has led to Infinity being an official “FANUC Authorized System Integrator”.
Extreme versatility is built into the design of the R10SW, either vacuum or servo gripper end effectors can be equipped on the palletizer, allowing for high-speed stacking capabilities on a wide range of products, including cases, bundles, and DRP.
The versatility of the R10SW is complemented by robust performance as the palletizer has a full unit load total height of 110 inches.
Infinity engineers prioritized operator convenience and safety in the design of the R10SW, resulting in a machine that is as safe as it is accessible. The palletizer features multiple safety zones, separated by access gates, allowing for safe up-close monitoring of production. Access to hard-to-reach areas of the machine has also been improved.
As tissue converters throughout the world continue to embrace automation, flexibility is as essential in the production’s end-of-line as it is in the converting and packaging process. The R10SW brings Infinity’s signature innovative engineering and robust build quality to the world of palletizing solutions, making the production end-of-line safer, smarter, and as flexible as the rest of your line.
Infinity Machine & Engineering Corp. to exhibit at Tissue World 2024
From January 31st to February 2nd, Infinity Machine & Engineering Corp. will return to the Miami Beach Convention Center to exhibit at Tissue World 2024.
The previous show, Tissue World 2023, took place in Dusseldorf and brought together tissue industry professionals across Europe. This year’s exhibition promises to draw representatives across the North American, Latin American, and South American tissue markets.
At this year’s exhibition, Infinity will officially launch their line of palletizing solutions, expanding the Infinity product line beyond primary and secondary tissue packaging.
Responding to consumer demand, Infinity palletizing solutions can be integrated with Infinity packaging lines, enabling Infinity machinery to automate every step of the tissue production process after the log saw.
A key aspect of Infinity’s palletizing solutions is their modularity. The unit is made up of modular palletizer sections that can be arranged into countless different layouts in order to accommodate production requirements, as well as facility limitations. The flexibility created by these palletizer sections make it perfect for a multitude of product lines, from single product, to large-scale, multi-line operations.
The palletizer segments offered by Infinity include automatic slip sheet placement, integrated labeling, and fully automatic, fully servo stretch wrapping. All designed to provide extreme efficiency and versatility in a minimal amount of space.
To learn more about the palletizing solutions offered by Infinity, as well as new developments among its existing roster of machinery, stop by the Infinity booth located at space B30.
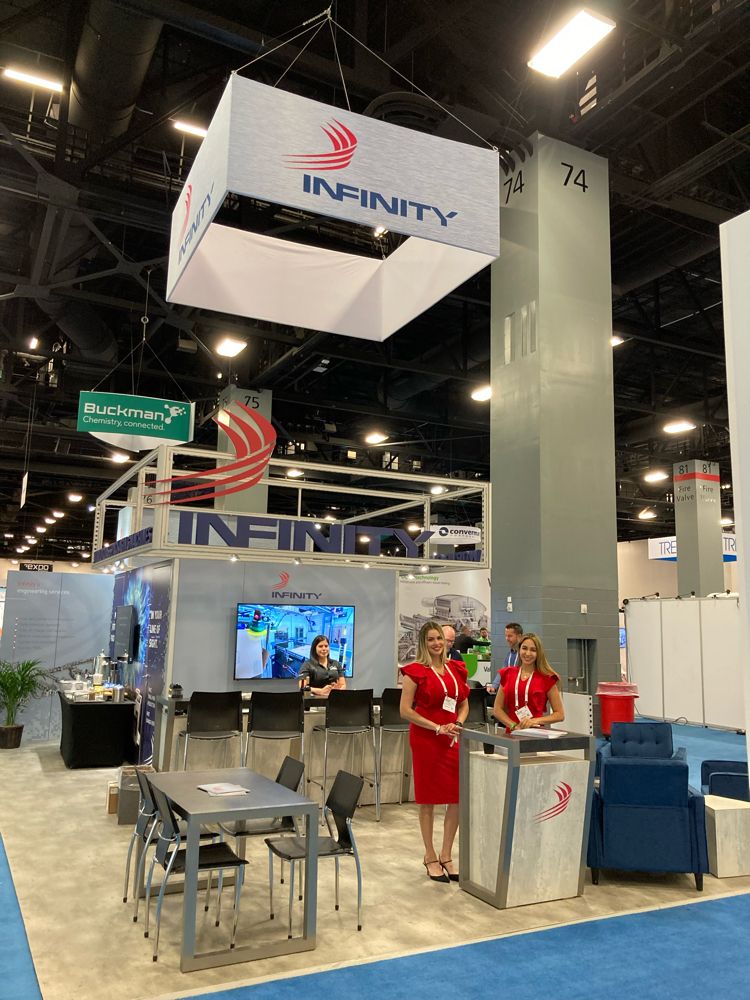
Infinity Machine 20th Anniversary
In 2004, Scott Santaga, Jeffery Cogswell Thomas Wegner and Douglas Wegner founded Infinity Machine & Engineering Corp. with a simple guiding principle, to serve the customer. While a lot about Infinity has changed since 2004, the commitment to serve the customer never has.
Since the beginning, Infinity has been defined by the entrepreneurial spirit of its founders. What began as a company that operated out of a 9X15 square meter facility has grown to be the premier name in automated tissue packaging.
Originally, Infinity was founded as a company that would design and build poly bundlers, however plans changed when Infinity’s first order was for a casepacker. Infinity’s founders adapted to the needs of the customer and designed a casepacker that was flexible and operator friendly. The first Infinity casepacker is still in operation today, a testament to its design and build quality.
Throughout its 20-year history, Infinity has continuously pushed the boundaries of what tissue packaging machinery can be capable of. Debuting in 2005, Infinity’s signature Infusion modular system utilizes interchangeable packaging modules and a fixed, common infeed unit. This revolutionary design allows for casepacking, bundling and bagging to occur all in one place, providing unmatched flexibility for converting lines. The Infusion modular system has become a global success with systems installed across North America, Europe, and Asia.
In 2010 Infinity added the talents of Italian technical specialist and sales staff with the creation of Infinity Italia. With the addition, American and Italian engineers combined their expertise to develop Infinity’s first poly wrappers. Among these wrappers was the Solo 250, a single roll wrapper capable of running production speeds of 250 rolls a minute. Since expanding the product line, nearly 200 poly wrappers have been installed, making them an iconic part of Infinity’s product mix.
Infinity has not been limited to innovations in machinery, the company also responded to their customer’s desire for more environmentally conscious packaging solutions. In 2020 Infinity partnered with Little Rapids Corp. to develop and test Ecova, a 100% plastic-free paper overwrap made from recycled materials. Since the debut of Ecova, Infinity has continued to prioritize sustainability with continual investment in ecologically focused research and development.
With machinery installed in over 20 countries, across every continent except Antarctica, infinity has established itself as the international industry leader in automated tissue packaging machinery. From France to South Korea, Infinity customers know that Infinity provides quality machinery and unparalleled customer service.
To accommodate the company’s rapid growth, Infinity’s headquarters has been expanded twice since it opened in 2008. The most recent expansion, which took place in 2020, increased the size of the facility to 16,000 square meters. Infinity has also increased its staff to over 200 employees between its Italian and American operations, nearly doubling in size from the total five years ago. However, the success of Infinity cannot solely be measured in facility expansions, or employee growth, it is also measured in the pride Infinity employees have in building the best tissue packaging machinery on the planet.
Infinity has undergone a multitude of changes throughout its 20-year history. However, through multiple expansions to its roster of machinery, continuous increases in international sales, and breakthroughs in ecological packaging, one thing has remained constant, Infinity’s commitment to serve its customers.
Serbian Tissue Manufacturer Invest in Infinity Machinery
Drenik ND d.o.o. a Serbian manufacturer of hygienic paper products and one of the largest cellulose manufacturers in Southeast Europe, has purchased six machines from Infinity Machine & Engineering Corp. The sale was completed in collaboration with Impex Continental.
To keep up with their increased production demands and maintain their strict quality standards, Drenik selected Infinity’s most recent machine releases, the VISION G3 multipack wrapper and the Optic M1 poly bundler. The two VISION G3s and four Optic M1s will be installed at Drenik’s facility in Belgrade, Serbia. These machines will continue the trend of Infinity’s recent rapid growth in Europe. In the last six years, Infinity has more than quadrupled its machine presence in Europe, supplying nine European countries with automated tissue packaging machinery.
Infinity’s VISION G3 multipack wrapper boasts an array of new innovative features. A patent pending telescoping poly unwind enables faster production speeds while improving pack quality. The Vision G3 can also produce poly wrapped, paper wrapped, paper tucked and facial tissue packs, providing Drenik with unparallel packaging versatility.
The Optic M1 poly bundler is a perfect fit for Drenik’s line as it is designed to produce large format bundles, common in the European market. The unique interchangeable upender and flight bar units on the Optic also appealed to Drenik as they allow for the creation of both “core up” and “core down” pack configurations.
When looking for the right partner for their largest investment of the year, Drenik was drawn to Infinity in large part due to their shared enthusiasm for success and innovation. Founded in 1995, Drenik started as a company that solely manufactured diapers and sanitary pads, however, the company soon expanded into bathroom tissue and household towel rolls. Today, Drenik produces over 100,000 tons of tissue a year and employs over 800 people between its facilities in Serbia and Hungary.
Throughout Drenik’s growth, they have been a company driven by sustainable practices, this drive goes hand in hand with Infinity’s expansive sustainability initiatives. The Optic M1 and VISION G3 can be equipped with IE3 and IE4 rated motors, which operate at a higher efficiency while using less power. The VISION G3 can also wrap rolls in paper, reducing plastic consumption and promoting more ecological packaging.
Drenik’s investment in Infinity machinery ensures that they will have the flexibility to meet any possible market need, while promoting sustainable practices.
Infinity Debuts New Pivoting Servo Merge Diverter
Infinity Machine & Engineering Corp. is proud to release the newest addition to its line of servo diverters, the Pivoting Servo Merge.
Specifically designed for facial tissue converting lines, the PSM diverter merges two layers of product into one layer, or one layer of product into two, ensuring a balanced, precise output for production.
The PSM features fully automatic guardrails, ensuring changeovers between flat tissue packs and cube tissue packs are simple and quick.
Another aspect of the PSM that puts customer convenience at the forefront is the machine’s ability to operate with its own individual PLC, or to be integrated with an existing PLC. Whatever a converting line requires, the PSM can be incorporated with ease.
Infinity’s newest diverter also features electronic gearing, allowing the operator to have complete control over the gap size between packs, and in turn, control over product orientation. With the PSM, product is merged, distributed, and controlled all in one compact space.
The PSM diverter from Infinity is the perfect distributor to make facial tissue lines faster, smarter, and more versatile.
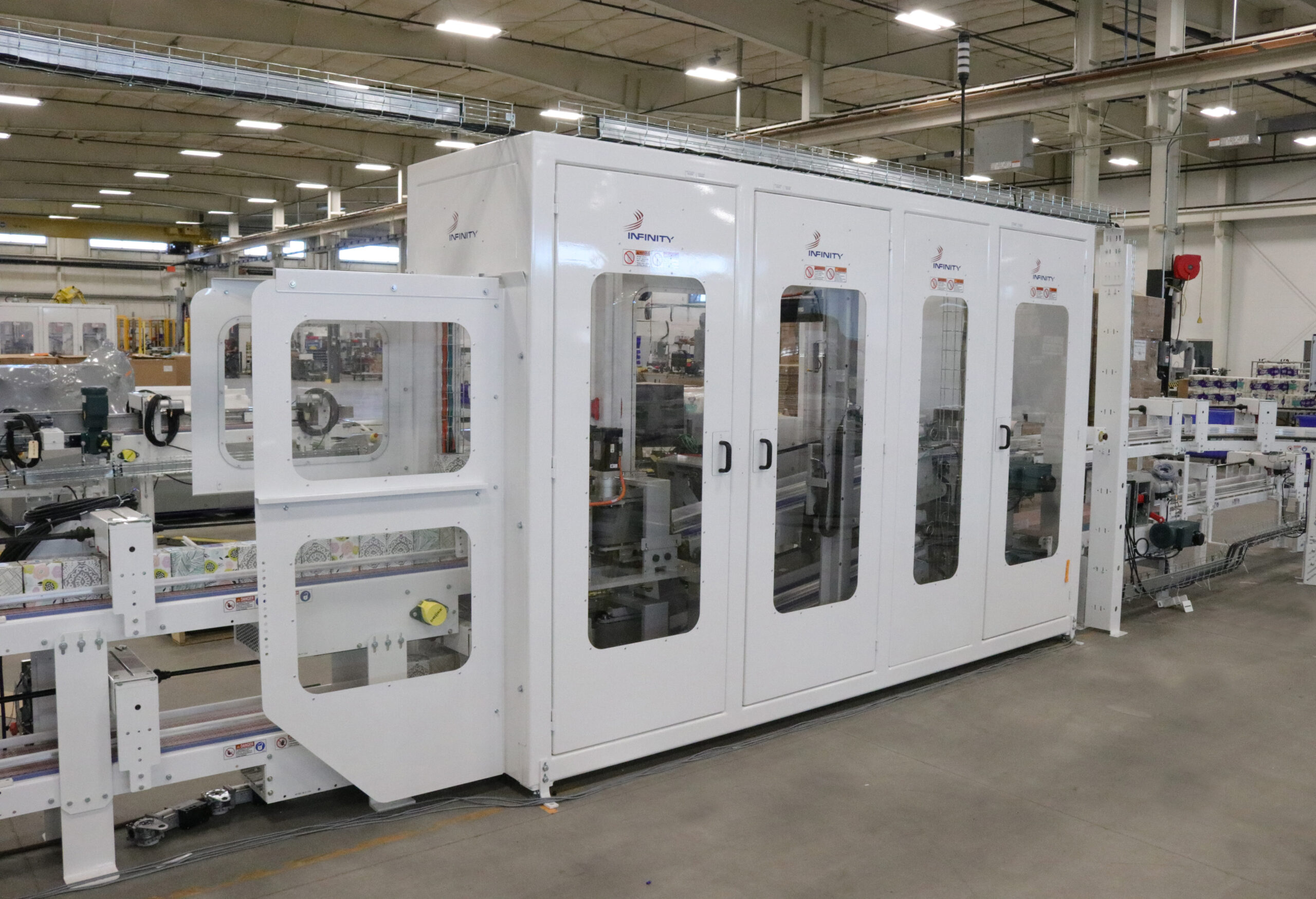