Eliminating Machine Maintenance Downtime
With around-the-clock automated operation quickly becoming the global norm in production lines, the negative effects of unscheduled machine downtime become increasingly more pronounced.
High-quality machinery is no longer enough, production lines need reliable customer service and quick turnarounds. This is why Infinity Machine & Engineering’s technical services are designed not just to resolve unplanned maintenance issues but eliminate them entirely.
Infinity prides itself on offering a range of preventative maintenance plans to keep machines and the companies that own them at optimal performance. A fixture of these plans is onsite machine audits performed quarterly, semiannually, or annually. These audits include a thorough inspection of all machines, documented service reports with recommendations after each visit, and additional machine training after the audit’s completion.
However, Infinity’s preventative maintenance begins before the machine leaves the facility. Every machine built by Infinity is put through a rigorous factory acceptance test, testing the customer’s exact specifications, and often running the customer’s actual product. This process ensures the machine is ready for installation and operation as soon as it is delivered. Furthermore, Infinity’s staff boasts a combined 65 years of packaging machinery installation experience, ensuring machine installation time is reduced to a minimum.
Another customer-focused technical service Infinity offers is operator and maintenance technician training. Technician training can be customized based on customer needs, including mechanical training on the customer’s existing Infinity
equipment, and electrical and E&I training. Offerings for Mechanical training include mechanical prints, parts search, rebuilding of assemblies, maintenance inspections, and lubrication routes. Electrical training covers electrical prints, parts search, PLC troubleshooting, replacement parts, and inspections.
To accommodate the round-the-clock production schedule of our customers, Infinity provides 24/7 on-call customer service. Field services techs can be at a customer’s mill within 24-36 hours after a call. Furthermore, Infinity does not charge extra for weekend work from their field service techs, whereas other
companies often charge double time on Sundays.
Another facet of Infinity’s technical services is an extensive spare part inventory. Between their Bologna and Green Bay facilities, Infinity has 20,000 spare parts on hand. There is also a dedicated expedited shipper for emergency situations so
crucial parts can be ordered at a moment’s notice.
Infinity takes consumer convenience in spare part offerings to the next level with predictive maintenance part kits. Through engineering, parts research, and mechanical knowledge of equipment, these kits are designed to maintain full runnability without unplanned downtime. Infinity’s predictive maintenance part kits are customized with common wear parts for all Infinity machine models. These kits also include a parts breakdown list, mechanical prints, and a standard procedure manual to assure the work is done to OEM spec. These give technicians the proper paperwork and parts to ensure the job will be completed properly and in a timely manner.
Infinity was created with a simple vision, to serve the customer, and the technical services offered by Infinity embody that vision. Machine audits that identify issues before they happen, a dedicated 24/7 customer support team, and an extensive spare part inventory all contribute to making this vision reality. When you buy Infinity, you buy peace of mind.
Infinity Euro Expansion
Since 2017, Infinity Machine & Engineering has more than quadrupled the number of machines it has supplied to European tissue plants.
While the American/Italian packaging machinery company has had a large presence in North America for over a decade, as of 2017, its sales in the European market were limited to several machines throughout Italy, Russia, and Slovakia. By the end of 2022, Infinity is scheduled to install over four times the amount of machinery it previously had in Europe, while also expanding sales into six additional European countries: France, Germany, Netherlands, Poland, Spain, and the United Kingdom.
Infinity’s recent rapid growth in the European tissue packaging industry can be attributed to a variety of factors, chiefly among them, the global positioning of the company and the recent increase of Infinity’s manufacturing capabilities.
Infinity is uniquely situated to serve the global market as it has facilities in the two global hubs for tissue paper production, Green Bay, USA, and Bologna, Italy. Infinity’s Italian operation specializes in sales and technical servicing, making Infinity an extremely desirable supplier of machinery for the European tissue industry.
Furthermore, in 2020, Infinity completed the construction of an 8,900 square-meter expansion of its Green Bay facility, allowing for Infinity to offer increased manufacturing capacity to their customers.
Combining Infinity’s global positioning and increased production capacity with the signature build quality and customer service that has made Infinity machinery famous worldwide, it is no surprise that Infinity is one of the fastest-growing suppliers of automated tissue packaging machinery in Europe.
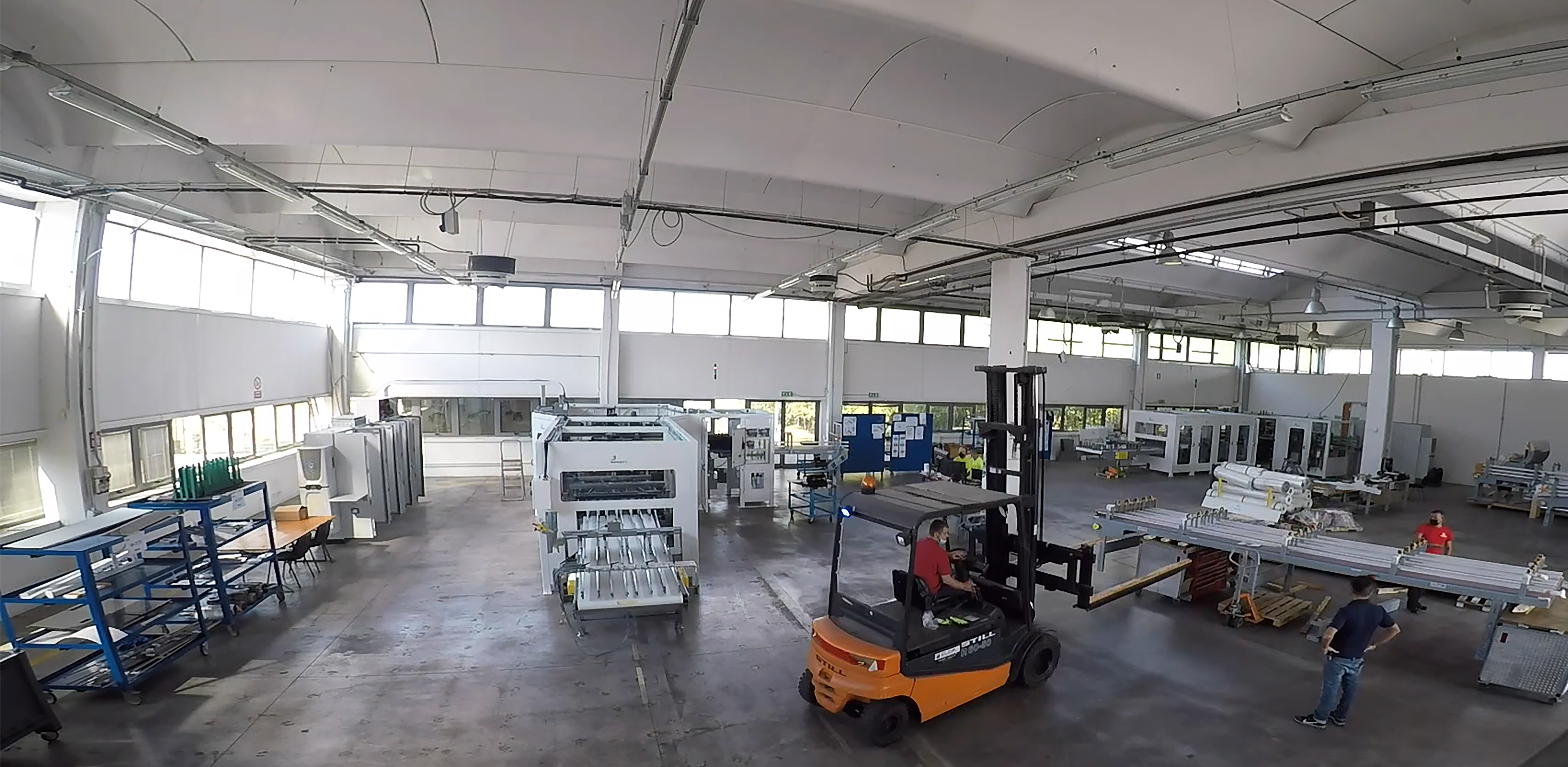